Valves are essential components in many industrial applications, including the refining and chemical industries. They play a crucial role in controlling the flow of various fluids, gases, and other materials. Over time, ball valves have emerged as a popular choice for these industries due to their superior sealing capabilities and reduced emissions. When it comes to choosing ball valves for these applications, selecting the right seat material is of utmost importance. In this blog, we will discuss the different ball valve seat materials available and what factors should be considered when selecting them for industrial applications.
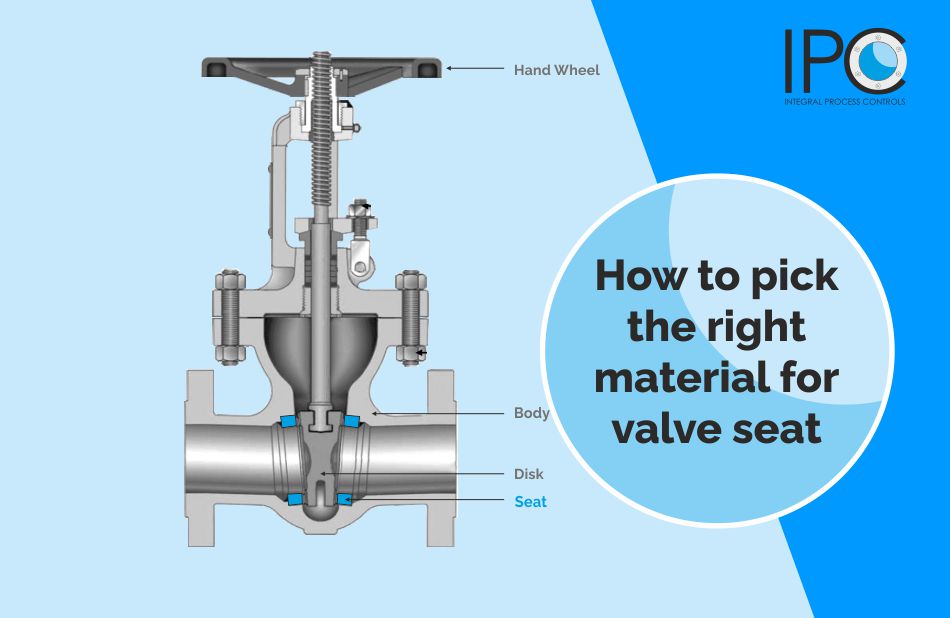
Soft Seat Segment Ball Valve Selection
Ball valve seat materials come in many varieties, and each one has its own pros and cons. When selecting a ball valve seat material, several factors need to be considered, such as temperature range, chemical compatibility, pressure rating, wear resistance, and more. A common approach when selecting ball valve seats is to break down the options based on application temperatures. The three common groups of ball valve seat materials are high-temperature materials, moderate-temperature materials, and low-temperature materials.
High-Temperature Materials
High-temperature materials are selected for applications where the temperature of the medium being controlled is over 400°F. The most common high-temperature materials used in ball valve seats are PTFE, PEEK, and PFA. PTFE is often used for high-temperature applications due to its excellent chemical resistance and low friction coefficient, allowing it to maintain its sealing abilities even at extreme temperatures. PEEK is often chosen for high-temperature applications because of its excellent dimensional stability, chemical resistance, and low thermal expansion coefficient. PFA is an excellent high-temperature material as it can withstand temperatures up to 500°F while maintaining good chemical resistance.
Moderate-Temperature Materials
Moderate-temperature materials are used when the temperature of the medium being controlled ranges between 200°F to 400°F. The most common moderate-temperature materials used in ball valve seats are TFM, PFA, and PEEK. TFM is commonly used for moderate-temperature applications due to its high-temperature range and excellent dimensional stability. PFA is often used in moderate-temperature applications because of its excellent chemical resistance and broad range of useable temperatures. PEEK is also an excellent choice for moderate-temperature applications due to its dimensional stability, chemical resistance, and low coefficient of friction.
Low-Temperature Materials
Low-temperature materials are used where the temperature of the medium being controlled is below 200°F. The most common low-temperature materials used in ball valve seats are UHMWPE, Nylon, and Delrin. UHMWPE is a popular choice for low-temperature applications due to its low coefficient of friction, chemical resistance, and excellent impact resistance. Nylon is used in low-temperature applications due to its good chemical resistance, low coefficient of friction, and affordable price point. Delrin is a low-temperature material that offers good wear resistance, low friction coefficient, and excellent chemical resistance.
Conclusion
When selecting a ball valve seat material, it's crucial to consider the application requirements to ensure long-lasting and reliable operation. By understanding the different ball valve seat materials and their characteristics, you can make an informed decision when specifying and ordering ball valves for your industrial applications. High-performance ball valves, such as the soft seat segment ball valve, provide excellent sealing and emissions control capabilities in the refining and chemical industries. Look for a trusted partner that can help you assess your needs and provide cost-effective solutions that meet your valve requirements.